La instrumentación y control, desde el punto de vista ingeniería, define el nivel de automatización de cualquier planta de proceso e instalación industrial, en donde dichas plantas están destinadas a la elaboración de uno o más productos sean para satisfacer un servicio básico del hombre o para la elaboración de la materia prima requerida por otra planta o industria. En los procesos industriales influyen alguna variables, las cuales necesitan ser controladas y monitoreadas con cierta frecuencia con la intención de conocer su comportamiento y como esta podría afectar la variable de proceso, si bien esto es cierto, también lo es el hecho de que estas variables, el la mayoría de los casos, resultan ser las variables de proceso y de esta manera se requiere llevar un control directo sobre ellas. Cabe destacar que, actualmente, existen instrumentos muy sofisticados, para el control de estas variables, las cuales brindan muchos beneficios, ya que son fáciles de utilizar y más importante aun permiten reducir los errores, brindando una medición más exacta para así ejercer un control con mayor precisión. Las múltiples ventajas que nos brindan los instrumentos se debe primeramente a la reducción de la mano de obra humana, la cual como todos sabemos presenta muchas limitaciones y por otro lado, facilitan la obtención de la señal de salida ya que muchos incorporan una circuitería mas completa, la cual permite la conversión de señales internamente para obtener el resultado directamente sin la necesidad de preocuparnos por el diseño de las interfaces para el acondicionamiento de la señal. Las variables estudiadas en los procesos industriales son: la temperatura, la presión, el caudal y el nivel. Para lograr el control de dichas variables es necesario conocer sus características y las del instrumento que se utilice para realizar la medición, con el objeto de enviar la información adecuada al instrumento de control. En este apartado se realiza el estudio y medición de la presión que se toma entre dos puntos, la cual es conocida como presión diferencial, utilizando un transmisor inteligente, con la finalidad de visualizar las diversas ventajas que este instrumento ofrece en cuanto a la reducción de los errores, mediante la calibración del instrumento.
1-. OBJETIVOS
1.1) General
-Calibrar un transmisor inteligente de presión (SITRANS P), para flujo y presión diferencial.
1.2) Específicos
-Realizar un montaje con el transmisor inteligente para presión diferencial.
-Visualizar las ventajas de ajuste y calibración del transmisor inteligente.
-Determinar el error de lectura haciendo uso del trasmisor inteligente.
2-. FUNDAMENTO TEÓRICO
Para la realización y comprensión de un trabajo practico, es necesario conocer una serie de términos relacionados al tema o al proceso estudiado, con la finalidad de entender su comportamiento y así emitir un juicio de valor de acuerdo a los resultados experimentales. Para la elaboración de esta práctica, los conceptos más importantes son:
2.1) Presión
Se puede definir la presión como la fuerza normal que se ejerce sobre una cierta área, y se mide en unidades de fuerza por unidad de área.
2.2) Medidas de Presión
Las medidas de presión comúnmente utilizadas en la industria son:
-Presión relativa o manómetro.
-Presión absoluta.
-Presión diferencial.
2.3) Presión Diferencial
2.4) Unidades de Presión
Las más utilizadas son “bar”, “kg/cm²”, “mm.c.a”, para la mayoría de los proyectos. En proyectos americanos la unidad de presión por excelencia es el “psi”.
2.5) Elementos Primarios
Son aquellos instrumentos que están en contacto con el fluido o variable, utilizando o absorbiendo energía del medio controlado para dar al sistema de medición una indicación en respuesta a la variación de la variable controlada. Cabe indicar que a los instrumentos compactos como manómetros, termómetros, transmisores de presión, etc. ya se supone que el elemento primario está incluido dentro del propio instrumento.
2.6) Transmisores
Son aquellos instrumentos que captan la variable de proceso, generalmente puede ser a través de un elemento primario, y la transmiten a distancia en forma de señal neumática (3-15 psi), electrónica (4-20 mA), pulsos,). Estos instrumentos dan una señal continua de la variable de proceso.
2.7) Transmisor
Es un dispositivo que detecta la variable de un proceso a través de un sensor y tiene una salida la cual varía su valor solamente como una función predeterminada de la variable del proceso. El sensor puede estar integrado o no al transmisor.
2.8) Transmisores de Presión
Este tipo de instrumentos de presión convierten la deformación producida por la presión en señales eléctricas. Una de su característica es la necesidad de incluir una fuente de alimentación eléctrica y tienen como ventaja sus excelentes características dinámicas, es decir, el menor cambio producido por deformación debida a la presión, es suficiente para obtener una señal perfectamente detectable por el sensor. Dentro de los transmisores los hay ciegos (sin indicador local) y con indicador local incorporado.
2.9) Indicadores Locales
Son aquellos instrumentos que captan la variable de proceso y la muestran en una escala visible localmente. Los indicadores locales más utilizados son los Manómetros (presión), termómetros (temperatura), rotámetros (caudal), etc. Normalmente estos instrumentos no llevan electrónica asociada, aunque también se consideran indicadores locales a los indicadores electrónicos conectados a los transmisores. Estos últimos pueden ser analógicos o digitales.
2.10) Sensor
Convierte una variable física (presión, temperatura, caudal, etc.), en otra señal compatible con el sistema de medida o control.
2.11) Señal de Salida
Señal producida por un instrumento que es función de la variable medida.
2.12) Variable Controlada
Dentro del bucle de control es la variable que se capta a través del transmisor y que origina una señal de realimentación.
2.13) Variable Manipulada
Cantidad o condición del proceso variada por el elemento o elementos finales de control.
3-. PROCEDIMIENTO EXPERIMENTAL
A continuación se muestra el diagrama esquemático requerido para la realización del trabajo práctico de laboratorio (Figura 1). Este diagrama muestra los equipos e instrumentos que fueron necesarios para la medición de presión diferencial utilizando el transmisor inteligente (SITRANS P), como se puede notar este esquema consta de varias partes entre ellas se encuentra: un compresor que fijamos a una presión constante indicada (1 bar), utilizando para ello la válvula de regulación del compresor, la siguiente etapa estuvo integrada principalmente por el transmisor inteligente el cual requirió, para su implementación, de una conexión como la que se muestra en la Figura 2, cabe destacar que la presencia de la resistencia se debe a la necesidad de realizar una conversión de voltaje a corriente ya que dicho transmisor se alimenta con corriente. En esta etapa también encontramos el manómetro patrón, en la cual se indicó la presión que variamos desde 0.2 bar hasta 1 bar en pasos de 0.2, con ello se pudo obtener la corriente proporcional a la diferencia de presiones entre la presión fijada del compresor y la indicada por el manómetro patrón, la cual se mostraba en la LCD del transmisor y a su vez se obtuvo valor de tensión que generaba el transmisor en la resistencia de 200Ω. El procedimiento experimental constituyo de 2 partes en las cuales se tomaron medidas de los mismos parámetros, la primera sin calibración y la segunda calibrando el transmisor para obtener una salida mas próxima a la real.


4-. RESULTADOS
4.1) PARTE I Sin calibración del transmisor inteligente
4.1.1) Mediciones directas
Los datos obtenidos por medición directa en el laboratorio fueron: La presión fijada en el compresor P1, las presiones indicadas por el manómetro patrón P2, la corriente proporcional a la diferencia de presiones entre el compresor y el medidor, mostrada en la LCD del transmisor I0 y el voltaje en la resistencia de 200Ω VR. Dichos valores se encuentran resumidos en la tabla que se muestra a continuación.

Para generar la tabla anterior se realizaron los cálculos de las presiones diferenciales (P12) entre el manómetro patrón y la presión fijada en el compresor, a su vez se calculó la corriente que generaba el transmisor (I1) ya que, en el laboratorio, se pudo medir el voltaje en la resistencia de 200Ω para cada valor de P2. A continuación se presentan una tabla con los valores calculados de I1=IR de acuerdo a los valores medidos de VR y P2.

-Para P2=0.2 bar, tenemos:
P12= 1 bar-0.2 bar P12= 0.8 bar
VR= 6.48 volts IR= VR/200Ω IR= 6.48/200 IR= 32.4 mA
Para satisfacer las peticiones del Post-Laboratorio se calculó:
a.) Las corrientes experimentales (It), la cual es proporcional a la diferencia de las presiones medidas es decir, proporcionales a P12.
Se utilizo la ecuación siguiente, la cual fue suministrada por el profesor:


Para demostrar esta tabla a continuación se presenta un cálculo:
-Para P12=0.8 bar, tenemos:
It= (19.96-4.0)*(0.8)/(0.8) + 4.0 It= 19.96mA
Es importante señalar que los datos que se cumplen para todos los cálculos son:
Imax = 19.96 mA Imin = 4.0 mA P12max = 0.8 bar
b.) Los errores entre It e I0.
A continuación se presenta una tabla donde se presentan estos errores.

Error =(32.4-19.96) * 100/(32.4) Error =38.39%
4.1.3) Gráficas de errores

4.2) PARTE II: Calibrando el transmisor inteligente para presión diferencial
4.2.1) Mediciones directas
Para llevar acabo esta parte de la practica se siguió una serie de pasos establecidos con la finalidad de calibrar el instrumento para obtener salidas mucho mas cercanas al valor real, cabe destacar que los parámetros medidos en este caso siguen siendo los mismos anteriores es decir, La presión fijada en el compresor, las presiones indicadas por el manómetro patrón, la corriente proporcional a la diferencia de presiones entre el compresor y el medidor, mostrada en la LCD del transmisor y el voltaje en la resistencia de 200Ω .Dichos valores se encuentran resumidos en la tabla que se muestra a continuación.
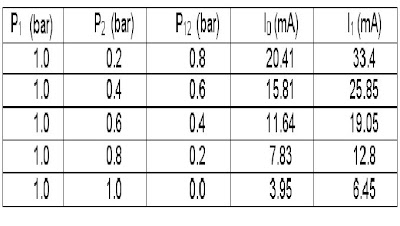
4.2.2) Cálculos Realizados
Similar a lo expuesto en la primera parte, se realizaron los cálculos de las presiones diferenciales (P12) entre el manómetro patrón y la presión fijada en el compresor, también se calculó la corriente que generaba el transmisor (I1) medida en la resistencia de 200Ω para cada valor de P2 y VR. Para la realización de dichos cálculos se aplicaron los mismos procedimientos de la primera parte. Los valores obtenidos fueron los siguientes: Para satisfacer las peticiones del Post-Laboratorio, en se calculó:
a.) Las corrientes experimentales (It), la cual es proporcional a la diferencia de las presiones medidas es decir, proporcionales a P12.
A continuación se presenta una tabla con los valores calculados de It de acuerdo a los valores de P12.

A continuación se presenta una tabla donde se presentan estos errores.


5-. ANALISIS DE RESULTADOS
En la primera parte del laboratorio se observa que a medida que aumenta la presión indicada por el manómetro patrón, la presión diferencial entre el compresor y dicho medidor se va reduciendo hasta llegar a cero; cuando ambos tienen el mismo valor de presión (1 bar), de igual manera la corriente proporcional a esta diferencia de presiones I0, también se va reduciendo, partiendo desde un valor máximo aproximado a 20 mA hasta llegar a un valor mínimo aproximado a 4 mA. Se puede observar una discrepancia entre el valor medido de I0 y el valor calculado mediante la aplicación de la ecuación dada para It, una de las razones para explicar estos resultados es el hecho de no haber calibrado el instrumento y por lo tanto, no es posible comparar los resultados con un patrón de mayor jerarquía que permita indicar si estos valores son aceptables para el instrumento o no, sin embargo es importante acotar que a pesar de la no calibración del transmisor se obtuvo una salida lineal.
Con respecto a los resultados de la segunda parte, los valores de I0 e I1 son mayores que las obtenidas en el proceso sin calibración, también es importante acotar que los errores entre I0 e It son mucho menores, sin embargo resulta curioso que dichos errores tiendan a ser cero en el valor máximo y mínimo de corriente, aumentan durante los dos valores intermedios ascendentes y luego sufre otro cambio brusco disminuyendo significativamente antes de alcanzar el valor máximo, aun así estos errores no llegan a alcanzar valores tan elevados como en la primera parte, así se puede decir que se pudo reducir los errores ya que el cambio no es tan brusco como en la primera parte, a su vez se tuvo una respuesta lineal
6-. CONCLUSIÓN
El transmisor inteligente para presiones diferenciales permite realizar mediciones de una manera sencilla, ya sus partes son fáciles de manejar y la circuitería necesaria para el funcionamiento de dicho transmisor no es compleja. Es importante realizar la calibración del instrumento antes de realizar cualquier medición ya que siguiendo este patrón es posible realizar una comparación entre lo que se esta midiendo y el valor de salida establecido para el instrumento, sin embargo es posible emitir un juicio importante con respecto a la diferencia entre calibración y al ajuste del instrumento, con respeto a los resultados obtenidos se puede concluir que ambas expresiones no quieren decir la misma cosa ya que se logra calibrar el instrumento por medio de la aplicación de una serie de pasas dados , sin embargo no se realizo el ajuste necesario para su utilización ya que se obtuvieron resultados con grandes errores de cero. Una vez mas la salida es lineal, esto constituye un aspecto muy significativo ya que no es necesario incorporar circuitería adicional para linealizar; como todos sabemos es mucho mejor trabajar con instrumentos lineales que con sus contrapuestos.
7-. RECOMENDACIONES
Siguiendo con los conocimientos adquiridos en otras asignaturas es importante tener en cuenta, a la hora de realizar un trabajo practico de laboratorio, las especificaciones técnicas de los instrumentos utilizados así como las normas y procedimientos establecidas por el docente durante la ejecución de la misma para cumplir y lograr con éxito los objetivos planteados al iniciar la practica. Es importante acotar que el proceso para tomar las mediciones fue un poco engorroso debido a las diversas limitaciones del laboratorio de instrumentación, por lo cual es necesario el mantenimiento frecuente del espacio físico y a su vez la integración de los estudiantes con la finalidad de cuidar y velar por el cumplimiento de las normas de buen uso del laboratorio.
8-. BIBLIOGRAFÍA
-Documentos en línea. Instrum01. Pdf
-Documentos en línea. FI01_es_2007_Kap02. Pdf
No hay comentarios:
Publicar un comentario